WHAT IS THE “#1 BEST STORAGE SOLUTION” FOR MY COMMERCIAL WORKSPACE?
by Scott Olpin, on August 6, 2020
INTRODUCTION
How easy would it be to point to a lineup of storage systems and instantly know: “That’s it, that’s the one that will work for me!”?
Unfortunately, it is not always that simple.
Drawing upon my 30 plus years’ experience in helping industrial, commercial, and healthcare clients find what works best for them, I will outline several storage systems and describe why they work best for certain business operations.
Let’s be honest, though, it is literally impossible to address every best solution for every business in every category. Instead, I have tried to address enough business categories and their best storage solutions that you can easily relate your particular business to, if not the exact same business.
There are three factors to consider before you can identify the “Number 1 Best Storage Solution” for your commercial workspace:
- Evaluating Your Space
- Evaluating Your Inventory
- Determining Your Budget
ARTICLE OUTLINE
First, I will discuss in more detail the three factors above. Second, I will offer some real examples of the best storage systems for real businesses and I will give you the “Number 1 Best Storage Solution” for that business category. Third, I will ask you to consider your "why" -- why do you want to upgrade or change to a different storage system? I will also offer possible solutions for your reasons.
Lastly, I will provide a “cliff notes” reference at the end of the article for all linked resources.
FACTOR TO CONSIDER #1: Evaluating Your Space
How much space do I have and what are its dimensions?
Your space layout and dimensions will largely determine what kind of storage system you can best utilize. Of course, if you have unlimited space, your options are limitless. However, for those who don’t have the luxury (99% of us, I presume), consider the following:
- Does your space have high ceilings? If so, your options for storage become greater as you can utilize the unused overhead space.
- Is your storage space on a second floor with access only by stairs or elevator? Limited or difficult access may affect the storage system you choose.
- Do you have obstructions such as fire sprinklers, utility panels, or structural support beams in your designated storage area?
- Can you re-arrange your personnel areas for better workflow and storage?
FACTOR TO CONSIDER #2: Evaluating Your Inventory
A. What is the size and required weight loads of the items needing storage?
A perfect example to illustrate how to store different size inventory and weight is the museum industry. A museum has a paper collection consisting of maps, drawing, and other important documents that are relatively light in composition. This flat collection will be best stored and preserved in a flat file or flat tray cabinet(s).
On the other hand, an archeological stone collection will require sturdy industrial shelving that can support bulky and heavy loads.
To further increase storage density and capacity in the same space, both the flat files and industrial shelving can be installed on carriages in a Mobile System to more than double the storage in the existing space.
Evaluation:
- For flat file storage such as maps, prints, photographs, coins and other flat objects, Flat File Cabinets, with the option to increase storage density by installing on a Mobile System is the “Number 1 Best Storage Solution” as it protects these collections, eliminates wasted space, and provides easy access.
- For bulky, heavy, oversized objects, Industrial Shelving, with the option to increase storage density by installing the shelving on a Mobile System, is the “Number 1 Best Storage Solution” as it can efficiently store bulky, heavy items up to 1,125 pounds per shelf. Note: Pallet racking will have additional weight capacity.
B. What is the volume and turnover of inventory or product to be stored? How many different skus are there? How often are storage items accessed?
I will illustrate a best storage system for the above considerations with a real example:
CASE STUDY: A large automotive distributor of cars and parts provides service to over 64 dealers. They have over 9,000 skus and need to timely pick and deliver orders for their 64 dealers.
Issue presented: High volume turnover, 1,000s of skus, constant inventory access, and timely delivery to dealers required.
Solution: VLM. Using 9 vertical lift modules (VLM), they are able to pick and ship out 140 parts orders a day. The order is loaded into the VLM at the software interface, the VLM automatically finds the tray where the part is located and delivers it to the operator at ergonomic height to pick. While the operator is picking that part, the VLM is locating the next part and delivering it to the operator on a second tray as soon as the prior part pick is completed, and so on.
Comparison with a horizontal carousel: Prior to installing the VLM units, this distributor used horizontal carousels which required ladders to climb and pick parts, presenting safety issues. In addition, the machinery required a very large footprint, spreading out horizontally using a large amount of floor space. The worker had to walk around the carousel frequently to find parts, the carousel did not tell you where the part was, but instead the operator located it on paperwork then had to physically find it, all of which was very time consuming.
Evaluation:
In this case the Vertical Lift Module is the “Number 1 Best Storage Solution” for this distributor. The advantages of the VLM are the fast and centrally located picking. No time is wasted walking to and finding parts throughout the warehouse as the VLM locates and delivers parts directly to the operator. All parts are stored in a much smaller footprint as inventory is stored vertically 35 feet (in this instance). Operator safety is increased due to no bending, twisting, or reaching to retrieve parts--all parts being delivered within arms’ reach by the VLM. Lastly, there are real cost benefits to this operation as inventory control, productivity and efficiency increase using a VLM.
Alternative “Best” Storage Solution:
By contrast, hypothetically, one of the dealers serviced by this same distributor may use Stationary Shelving and Modular Drawers in their service department to store all their small to medium parts, as their turnover, number of skus, and volume will not warrant the cost of automation.
However, not all is lost as the modular drawers installed in shelving provide a big benefit to this business with increased high-density storage (no wasted space), organization, and easy visibility with full extension drawers to facilitate picking of parts.
To achieve even further storage density and capacity, this hypothetical dealership may opt to store its parts and supplies by installing the shelving and modular drawers on carriages in a mobile system. By doing so, the dealership will more than double its storage capacity using the same amount of space.
Comparison with Standard Shelving Alone: A business that stores all parts, inventory, and supplies on standard stationary shelving only may be wasting the space between the top of the storage items and the bottom of the next shelf. Small to medium parts stored in boxes on the shelving and are not visible or easily accessible to the worker. Access is also made difficult by having to reach beyond the box at the front of the shelf to get to the box stored behind or underneath on the same shelf.
The wasted space, access, and visibility issues can be resolved by using full-extension modular drawers in the shelving which compact and organize more storage in less space, provide visibility, and easy access. For bulkier items though, stand alone shelving may be the optimum storage medium.
Evaluation:
In this case, modular drawers in shelving, optionally combined with a mobile system, is the “Number 1 Best Storage Solution” for this smaller dealer.
C. Are there special considerations for “how” items need to be stored?
What you store may mandate more specialty storage considerations. For example:
- Is tracking chain of custody with evidence a consideration, or tracking delivery and receipt of parcels important?
- Automated Locker Carousels provide software interfaces that will generate usage reports and access logs
- Similarly, Smart Lockers track the delivery and receipt of parcels, in addition to electronically notifying patrons when a package has arrived
- Do you need a temperature-controlled environment?
- Refrigerated Lockers preserve and secure your evidence
- Is your inventory highly susceptible to loss and/or theft?
- For industrial sectors you can use wire cages and guarding to limit access to your machinery, utilities, and storage areas
- For commercial applications, wire cages and lockers, and rolling security doors also provide security options for your storage items
- Do you need controlled access to storage for security purposes?
- Along with a variety of locker options for secured storage, there are also a variety of locker locks to choose from which provide options for keyed, keyless RFID, fob, and smart locks, which allow you varied levels of control over locker access
- Do you need temporary secure storage options?
- Day use lockers can provide temporary, secured storage for gym goers, staff, hotel patrons, visitors
FACTOR TO CONSIDER #3: What is My Budget?
Your budget will also drive your storage solution choice. I recommend you speak with a storage expert who can provide you with the information you need regarding storage system costs.
However, there is an important point to keep in mind when considering cost vs. budget. For example, when you choose any automated storage and retrieval system, your initial investment will be higher, in most cases, when compared to non-automated storage systems. However, make sure to analyze your return on investment (ROI). Often the initial investment will pay off in greater returns by having automated your production.
DETERMINE YOUR “WHY” AND SOLVE THE STORAGE NEED
Also important to know is "why" you are looking to change or update your storage systems:
You Need More Space
- Do you need more space for equipment or machinery?
- Is your space shrinking because of growth – where do you put additional staff and inventory?
Streamline My Operations
- Do you want to improve your picking for faster retrieval time?
- Is safety and ergonomics a factor?
- Could you benefit from better inventory control?
- Do you need improved security to prevent theft and loss?
DISCUSSION #1: You Need More Space
If you are running out of space in your facility, for any reason, oftentimes the most obvious, and more traditional solution, is to move to a larger facility or add-on to your existing facility. With the high cost of real estate, both of these proposals can be quite costly.
SOLUTION: Overhead and High-Density Storage Systems
Instead, consider these more cost-effective options for expanding your storage in your existing workspace:
Industrial, manufacturing and warehouse sectors:
Mezzanines and Catwalk Systems are ideal for increasing storage or personnel office floor space and storing inventory that is slower moving.
Stairs and lifts are required to access the items so fast-moving parts are not typically stored on the top level unless some type of automation or conveyor system is part of the mezzanine.
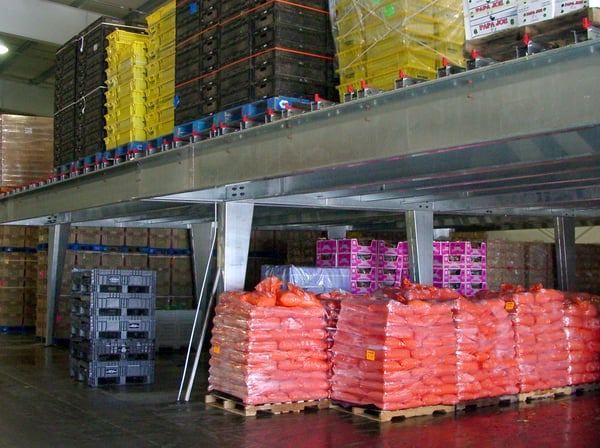
However, without adding to your overhead costs, you can double or triple your floor area turning unused air overhead into storage, office, or production areas with a mezzanine.
Catwalk systems allow you to stack shelving units up to 3 levels high while accessing each level with a “catwalk” that runs between the levels and shelving units.
Modular Buildings are ideal for expanding personnel and workspace.
Similar to the mezzanine concept space below the modular building can be utilized for other purposes. Likewise, modular buildings can be at the floor level and the space above used for storage or other purposes.
All Commercial Businesses:
Automated Overhead Storage makes use of overhead space for storage.
Store a multitude of items: bikes, boats, tires, clothing, equipment, inventory, etc. using a simple lift system. With the push of a button, items are lifted to be stored overhead or lowered to floor level for easy access.
High Density Mobile Shelving can double or even triple your storage capacity in the same space.
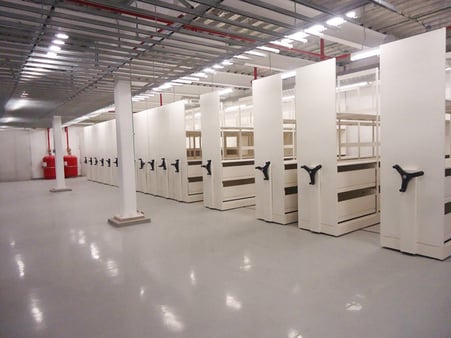
Storage capacity is increased by condensing shelving units together on a track, eliminating aisles, and storing higher vertically. A single aisle is opened either electronically or mechanically to easily access storage.
Both the Automated Vertical Carousel and Automated Vertical Lift can reduce your storage footprint by 75-90%! These automated systems use vertical space, anywhere from 7 feet to 50 feet high for storage and each system delivers the storage items directly to you at arms’ reach. However, they are not the ideal solution for every business that needs to store more in less space. They will be discussed further in the next section.
Evaluation:
When compared to expanding your building, or moving to a larger facility, in order to increase your storage space, your alternative “Number 1 Best Storage Solution” are overhead and high-density storage systems that will increase your storage capacity in the space you already have, such as those immediately discussed above: Overhead Storage, Mezzanines & Catwalks, High-Density Mobile Shelving, Vertical Lifts and Vertical Carousels.
Note: Expanding your facility or adding-on to your facility may still be the preferred and best option for you. The storage systems noted above (and below), however, will make the best use of your designated storage space in any building, new or existing!
DISCUSSION #2: Streamline My Operations
- Do you want to improve your picking for faster retrieval time?
- Is safety and ergonomics a factor?
- Could you benefit from better inventory control?
- Do you need improved security to prevent theft and loss?
SOLUTION: Automated Vertical Storage Systems
As discussed in the Case Study at the beginning of this article and just immediately above, Vertical Lifts are ideal for very active parts turnover, a large number of skus, and inventory control management. They are generally used in high volume picking operations, however, are also used in healthcare applications and are useful for large heavy bulky parts. Lifts can also be integrated with robotics. My article, "What is a Vertical Lift Module and How Does It Benefit My Business" will give you more detailed information on the Vertical Lift.
Vertical carousels, on the other hand, are a simpler automated solution and ideal for storing and retrieving anything you would store on stationary shelving (parts, inventory, supplies), tires, beds, carpet, textile, wire rolls, etc. This article, "What is a Vertical Carousel and How is it Used" gives helpful insight into the vertical carousel.
Why the lift and carousel are a good solution to streamline your operations and boost productivity
While each have their unique features, both the lift and carousel have similar benefits:
- By ergonomically delivering items within arms’ reach, employee injury is decreased and safety increased
- Inventory is secured from loss/theft
- Faster retrieval/picking times
- Less manpower needed for picking operations (the machines locate and retrieve for you)
- Increased picking accuracy
- Dramatic reduction in your storage footprint freeing up real estate for other productive uses
- Centralizing inventory on one location
- Better control over inventory management with automated software
Evaluation:
In order to streamline operations and boost productivity, both of which have profits at stake, your “Number 1 Best Storage Solution” is automated vertical storage systems such as the Vertical Lift or Vertical Carousel.
A word of caution: If you are a smaller business, your facility has low ceiling heights, and your inventory is relatively small and turnover is slow, this will probably not be the solution for you. High-density mobile shelving and free-standing shelving (see next section) may be your best options. A storage specialist can also help you determine what will work best for you.
WHEN NONE OF THE ABOVE ARE MY BEST STORAGE SOLUTION
While the storage systems discussed above offer great solutions, don’t feel left out if none of them are your best solution. Here are some additional options:
There is still, and always will be, a place for the great traditional storage system: Freestanding stationary shelving. There are different types of stationary shelving with multiple options to choose from, and a likelihood you’ll find your best storage solution. This article will help you navigate through your options: "Understanding the Different Types of Freestanding Stationary Shelving."
Evaluation:
When none of the previously discussed storage systems are your best solution, freestanding stationary shelving may very well be the “Number 1 Best Storage Solution” for you and provide you with the best storage option for your office, library, or place of business.
And There's More....
Other ideal storage solutions may require that storage is incorporated into your individual or team work spaces such as automotive service departments, electrical or parts assembly and repair teams. Automotive workbenches, work centers, and/or mobile carts may very well be the ideal “Number 1 Best Storage Solution” for you, fitting smaller and individual operations.
If your specialty is in labs or pharmacies, you need your work tools to be readily accessible, and you need flexible furniture systems that can repurpose, reconfigure and relocate as your needs and technology change, then modular casework may be the “Number 1 Best Storage Solution” for you.
“CLIFF NOTES” REFERENCE
Each of the following storage systems were addressed in this article to help you gain a greater understanding of each. For easy reference, they are listed and linked below in the order they appear above:
CONCLUSION
If you have gained a better understanding and some tools to navigate through the storage system industry to determine your best option, my goal has been reached. However, your unique situation may leave you with questions, or with the need to seek the help of a storage specialist. In either case, don’t hesitate to reach out. Our team has a combined experience of over 100 years in material handling solutions.
Cheers, Scott Olpin.
P.S. Is there any other storage topic you want to hear about? We welcome your suggestions or comments below.